On any type of refrigeration system, from small reach-in coolers all the way to large chillers, controlling the head pressure of the refrigerant is important. That’s because it helps keep the system operating properly in low ambient conditions — typically below 65°F for air conditioning and 55° for refrigeration systems.
Low load conditions can also affect system operations. Controlling the head pressure helps maintain pressure drop across the metering device and prevents the evaporator from freezing, in the case of air conditioning, and excessive freezing in refrigeration systems. Finally, it helps prevent flashing of the refrigerant in the liquid line while maintaining enough pressure for hot gas defrost and capacity control, if the system is so equipped, to ensure the system works properly. Air Cylinder Seals
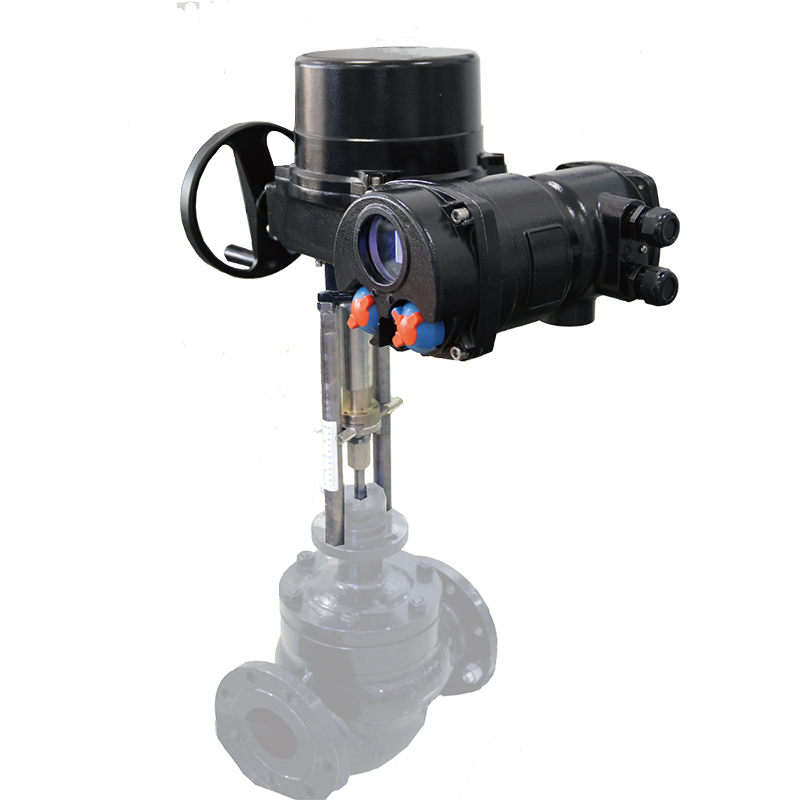
Quite often, the need to add head pressure controls is due to poor low ambient performance or replacement of a failed component. Once the need is established, the next step is determining the best type of head pressure control for each application. There are three basic types of head pressure controls, and each has advantages and disadvantages.
As the least complicated of the three methods, fan cycling can be done in one of two ways — refrigerant pressure or temperature. With multiple condenser fans, fan cycling can be as simple as using a temperature sensor or thermostat to keep the condenser fan from running below a preset temperature. For single or even multiple condenser fan units, the head pressure can often be maintained within a certain range using a pressure control to cycle the fan motor on and off.
One problem with this method is the number of times the motor has to start and stop, which results in short cycling and can shorten the life of the motor and the pressure control. Another disadvantage can be that the pressure control could leak refrigerant or simply fail due to repeated cycling.
Using a pressure switch-controlled relay can help with this and may be necessary for a three-phase motor or for higher amp draw motors. With this control, select the proper switch based on the type of refrigerant used and the amp draw of the motor. Next, if the pressure controls are adjustable, set up the cut in and cut out points to minimize short cycling. Finally, verify the cut in and out set point pressures with a gauge and add an access tee to maintain a service port, if needed.
Always install the refrigerant connection of the control on the liquid line, never on the hot gas line.
Forcing less air across the condenser coil and reducing heat exchange by slowing the condenser fan has the effect of keeping the head pressure higher and more stable. Because there are a variety of controls to accomplish this, the challenges can be deciding on the right one for the motor and the proper setup.
Three-phase motors may require a variable-frequency drive (VFD) and a pressure/temperature transducer, and the motor must be drive rated. Before deciding which is best to use, first determine the type of bearings on the motor. Remember, sleeve bearing motors must operate at higher RPMs than roller bearing motors. Then, find the answers to the following questions:
Pressure-regulating valves, which are designed to control the head pressure by maintaining a constant flow of liquid to the metering device, are another option. There are three different types of pressure regulating valves, and they are factory installed and preset.
These valves work by bypassing discharge pressure to the top of the receiver, thereby maintaining a higher condensing pressure that causes the condenser to flood with liquid and prevent flashing of the refrigerant in the liquid line. These types of controls only work with a system that has an expansion valve and liquid receiver that is sized large enough to handle the required excess refrigerant. Some are field adjustable, and most are refrigerant specific.
Determining which of the three types to use, system compatibility, and setup can be challenging. Field installation requires removing the charge and piping them into the system.
When adding head pressure control, the deciding factors on which option is best often comes down to the time the system is out of service and costs — both the initial cost of the controls as well as the cost of labor to install and set it up. If this is a new or replacement install, it may be better to select factory-installed equipment.
So how to choose which is best? For smaller systems, the more logical choice may be the least expensive — a pressure control for condenser fan cycling. Using speed controls provides for smoother operating pressures and fewer motor starts and stops. However, installing or replacing pressure regulating valves requires the most labor and the refrigerant must be recovered. If the unit has a failed pressure regulator, replacing it may provide the best system operation. All these factors must be considered when selecting the right control for the job.
You must have JavaScript enabled to enjoy a limited number of articles over the next 30 days.
Sponsored Content is a special paid section where industry companies provide high quality, objective, non-commercial content around topics of interest to the ACHR News audience. All Sponsored Content is supplied by the advertising company. Interested in participating in our Sponsored Content section? Contact your local rep.
On Demand In this webinar, we go through the recent updates on R-290 natural refrigerant, and the impact it will have on the HVACR industry.
Homeowners are demanding energy efficient solutions and a smart thermostat is the perfect compliment to a heat pump installation, enabling savings and efficiencies.
Copyright ©2023. All Rights Reserved BNP Media.
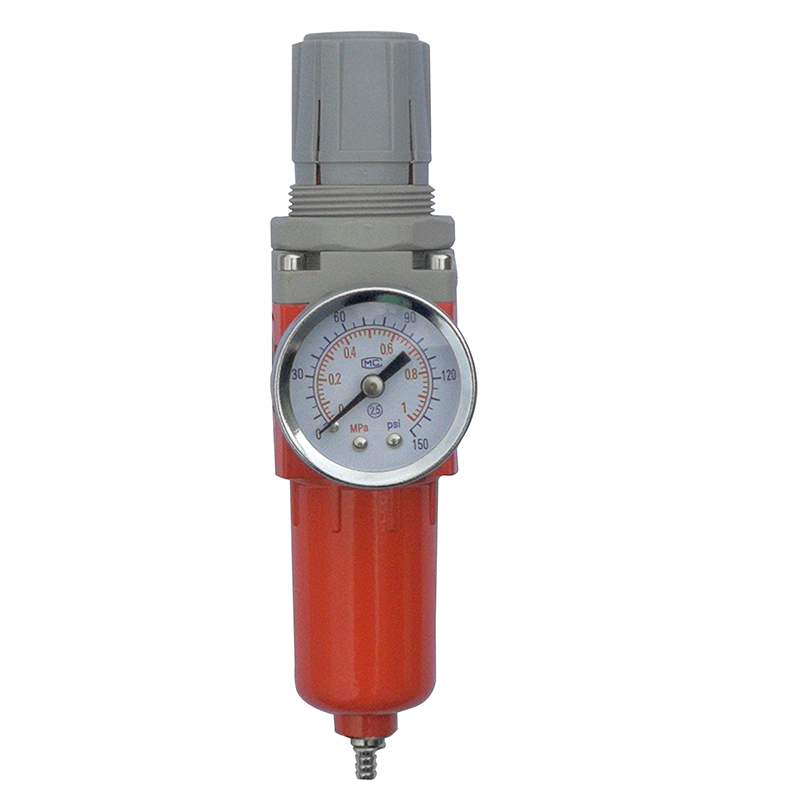
Solenoid Valve Design, CMS, Hosting & Web Development :: ePublishing